When it comes to Diesel engines, forged steel pistons are the next frontier in performance, and Diamond is leading the way. Take a look at the most innovative Diesel racing pistons on the market.
Forged steel pistons pretty much own the industrial diesel market. They are favored because of the severity of the combustion environment and the associated challenges it presents to optimum performance and long-term durability. Steel pistons are significantly stronger than aluminum and they offer potential combustion and thermodynamic advantages that favor fuel consumption and reduced emissions levels. Improved ring land wear characteristics and piston cooling are two of the major advantages attributed to steel pistons.
As the OEM’s continue to push their engines to higher and higher ratings, they have reached the limits of what cast factory pistons can stand. Then zealous consumers decide they can do even more with different tuning strategies and add-on parts. Failure lurks like the grim reaper in these scenarios. The need for tougher pistons in extreme applications leads us back to a steel piston configuration that is more suited to severe operating environments. These conditions are particularly hard on piston rings
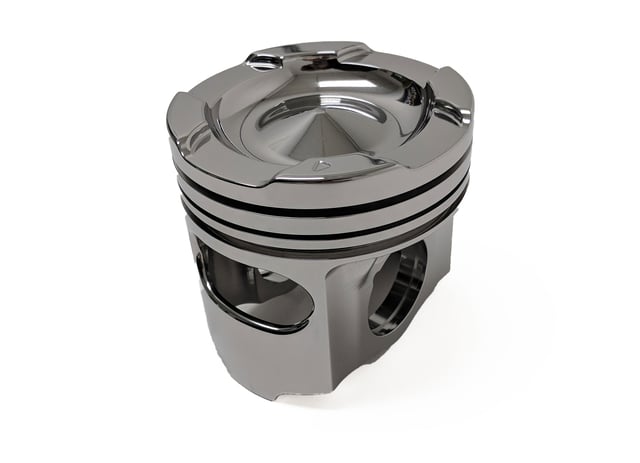
A stable ring environment is crucial to ring performance under the high cylinder pressures that diesel engines create. If ring performance deteriorates, combustion efficiency is compromised, and emissions tend to rise. A thermodynamically stable piston reinforces ring performance and reduces friction. Steel pistons also enjoy the advantage of large internal cooling galleys to help stabilize piston temperature and thus ring performance within the ring grooves and against the cylinder walls. Steel pistons also expand and stabilize at close to the same rate as the cast iron engine block, further contributing to improved ring seal and overall emission characteristics.
The benefits of steel pistons in severe duty applications are difficult to ignore. The weight difference would seem substantial, but that is mitigated by the hollow spaces for the cooling galleries and the elimination of mass in areas where high strength is unnecessary. And it isn’t a major factor in commercial applications, because most powerplants are relatively low speed engines operating well below 3,500 rpm. Since the coefficient of thermal expansion in steel pistons is equivalent to that of the cast iron engine blocks, maintaining consistent component clearances is easier and more reliable.
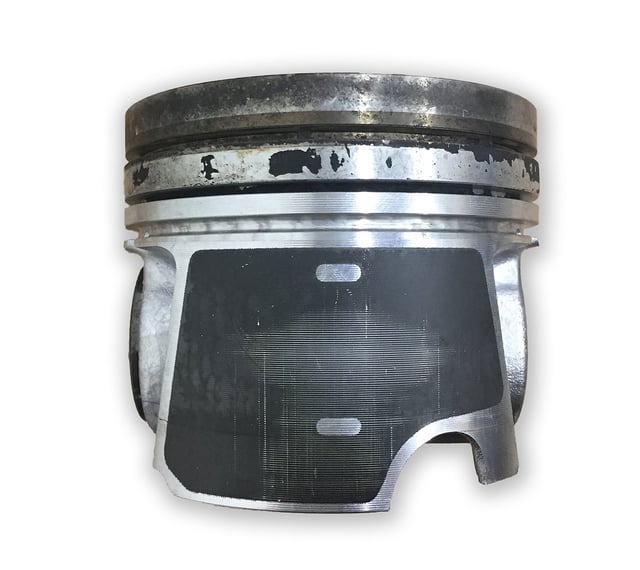
On the downside, steel pistons are heavier which increases parasitic drag. They are also more difficult to machine, particularly in large numbers as in, for example, the domestic pickup truck market. That’s a primary reason for the use of cast aluminum pistons with steel ring groove inserts in diesel pickup engines. Factory cast aluminum pistons are manufactured with steel ring groove inserts to resist the severe operating environment. But, as truck owners modify their vehicles for more power, higher cylinder pressures can cause factory pistons to fail.
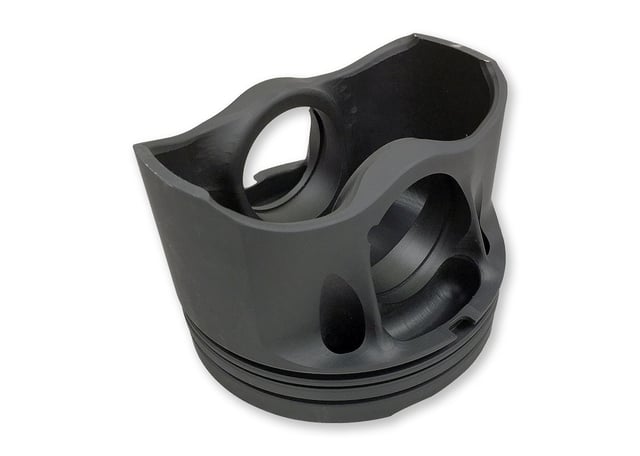
Diamond Pistons addresses ring groove deterioration by forging its factory replacement pistons out of billet 2618 aluminum with the addition of its exclusive Type III Hard Anodize Coating. The superior strength of the billet material with coating reinforcement makes these pistons plenty tough for the performance builds on Duramax, Power Stroke and Cummins diesel engines.
High cylinder pressures, heat, and erosion from high injection pressures are the core contributors to diesel engine distress. Diesels operate with compression ratios anywhere from 16:1 to 20:1. That helps improve their thermal efficiency, but it also creates massive cylinder pressures that can range from 4000 to peaks of over 8000 psi. That kind of pressure creates abnormally high temperatures. It requires oil cooling to dissipate the heat and control component thermal expansion. Supplemental cooling is also necessary to cool the rings and prevent them from losing shape and tension.
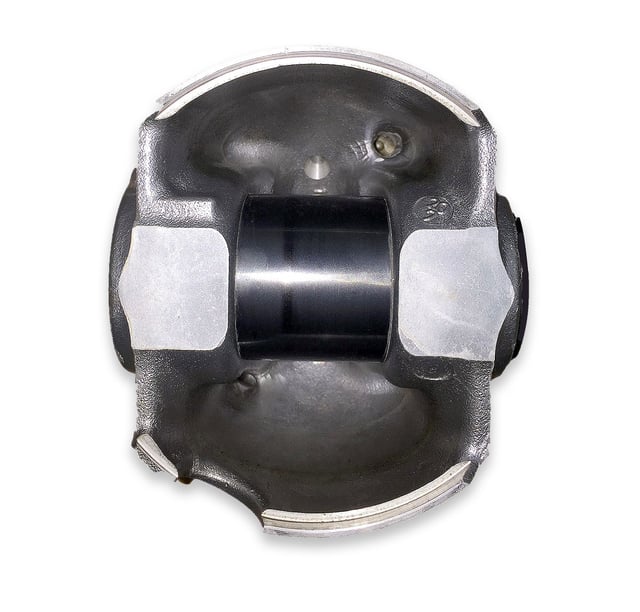
OEM Steel pistons have oil cooling galleries (when applicable) in the top of the piston to draw heat off the rings. Oil is sprayed into cooling galleries on the bottom of the pistons to remove heat. Cooling galleries typically reduce the top ring temperature by up to 100°F, which leads to better sealing and longer ring life. Heavy-duty, high-output commercial and truck engines often use two-piece “articulated” steel pistons with steel crowns and aluminum skirts or one-piece weldment pistons. Articulated pistons are two-piece pistons held together by the wrist pin. They allow the piston to handle higher loads than one-piece cast pistons and typically carry a very hefty wrist pin to mate the articulating crown and skirt components. One-piece steel pistons also offer advantages over one-piece cast aluminum, forged aluminum, and two-piece aluminum/steel pistons.
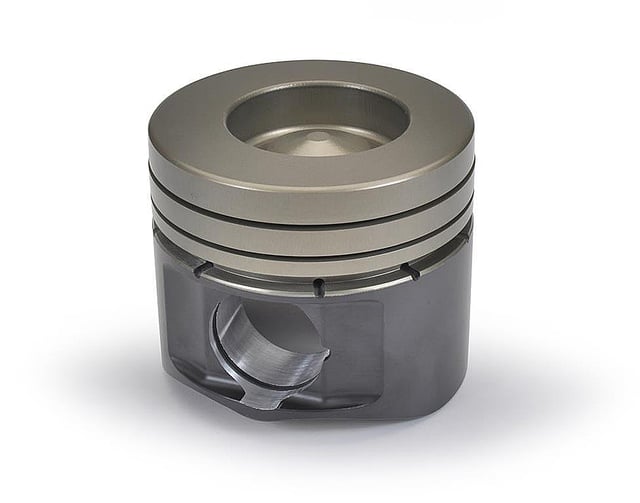
As a rule, steel pistons are more expensive and more difficult to make, but their practical application offers unparalleled strength and durability. The performance diesel marketplace has taken of note of this and has been retrofitting agriculture and industrial pistons into performance builds in the hopes of pushing their competition engines beyond the limits of what engines equipped with traditional pistons can handle—all in the hopes of making more power with longer life.
The main issue with this is that steel pistons are few and far between and don’t offer any room for customization in popular performance build configurations. Diamond’s unique design and manufacturing capabilities offers such customization for the performance diesel market. Diamond can design, engineer, and manufacture custom steel pistons for those extreme applications.
As the diesel market continues to emerge into the performance realm, the need for durable performance steel pistons is sure to expand. Diamond Pistons is positioned perfectly to assist OEM & prototype development outfits with rapid piston design and manufacturing assistance. Manufacturing steel pistons isn’t anything new for Diamond, however is relatively new for the performance market. Diamond’s state of the art CNC equipment, and manufacturing methodology allows for some lighter-weight performance diesel pistons that will take the abuse of the tremendous heat and cylinder pressures from these applications.